Before being adopted in this fashion, historically “clean coal” was used to refer to clean-burning coal with low levels of impurities, though this term faded after rates of domestic coal usage dropped. The term appeared in a speech to mine workers in 1918, in context indicating coal that was “free of dirt and impurities.”In the early 20th century, prior to World War II, clean coal (also called “smokeless coal”) generally referred to anthracite and high-grade bituminous coal, used for cooking and home heating.
Clean coal technology is a collection of technologies being developed in attempts to lessen the negative environmental impact of coal energy generation and to mitigate worldwide climate change. When coal is used as a fuel source, the gaseous emissions generated by the thermal decomposition of the coal include sulfur dioxide (SO2), nitrogen oxides (NOx), mercury, and other chemical byproducts that vary depending on the type of the coal being used. These emissions have been established to have a negative impact on the environment and human health, contributing to acid rain, lung cancer and cardiovascular disease. As a result, clean coal technologies are being developed to remove or reduce pollutant emissions to the atmosphere. Some of the techniques that would be used to accomplish this include chemically washing minerals and impurities from the coal, gasification (see also IGCC), improved technology for treating flue gases to remove pollutants to increasingly stringent levels and at higher efficiency, carbon capture and storage technologies to capture the carbon dioxide from the flue gas and dewatering lower rank coals (brown coals) to improve the calorific value, and thus the efficiency of the conversion into electricity. Concerns exist regarding the economic viability of these technologies and the timeframe of delivery, potentially high hidden economic costs in terms of social and environmental damage, and the costs and viability of disposing of removed carbon and other toxic matter. # ISO certification in India
In its original usage, the term “Clean Coal” was used to refer to technologies that were designed to reduce emission of pollutants associated with burning coal, such as washing coal at the mine. This step removes some of the sulfur and other contaminants, including rocks and soil. This makes coal cleaner and cheaper to transport. More recently, the definition of clean coal has been expanded to include carbon capture and storage. Clean coal technology usually addresses atmospheric problems resulting from burning coal. Historically, the primary focus was on SO2 and NOx, the most important gases in causation of acid rain, and particulates which cause visible air pollution and have deleterious effects on human health.# ISO certification in India
Technology
Several different technological methods are available for the purpose of carbon capture as demanded by the clean coal concept:
- Pre-combustion capture – This involves gasification of a feedstock (such as coal) to form synthesis gas, which may be shifted to produce a H2 and CO2-rich gas mixture, from which the CO2 can be efficiently captured and separated, transported, and ultimately sequestered, This technology is usually associated with Integrated Gasification Combined Cycle process configurations.# ISO certification in India
- Post-combustion capture – This refers to capture of CO2 from exhaust gases of combustion processes.
- Oxy-fuel combustion – Fossil fuels such as coal are burned in a mixture of recirculated flue gas and oxygen, rather than in air, which largely eliminates nitrogen from the flue gas enabling efficient, low-cost CO2 capture.
The Kemper County IGCC Project, a proposed 582 MW coal gasification-based power plant, was expected to use pre-combustion capture of CO2 to capture 65% of the CO2 the plant produces, which would have been utilized and geologically sequestered in enhanced oil recovery operations. However, after many delays and a cost runup to $7.5 billion (triple the initial budget), the coal gasification project was abandoned and as of late 2017, Kemper is under construction as a cheaper natural gas power plant.
The Saskatchewan Government’s Boundary Dam Integrated Carbon Capture and Sequestration Demonstration Project will use post-combustion, amine-based scrubber technology to capture 90% of the CO2 emitted by Unit 3 of the power plant; this CO2 will be pipelined to and utilized for enhanced oil recovery in the Weyburn oil fields.# ISO certification in India
An oxyfuel CCS power plant operation processes the exhaust gases so as to separate the CO2 so that it may be stored or sequestered. # ISO certification in India
An early example of a coal-based plant using (oxy-fuel) carbon-capture technology is Swedish company Vattenfall’s Schwarze Pumpe power station located in Spremberg, Germany, built by German firm Siemens, which went on-line in September 2008.The facility captures CO2 and acid rain producing pollutants, separates them, and compresses the CO2 into a liquid. Plans are to inject the CO2 into depleted natural gas fields or other geological formations. Vattenfall opines that this technology is considered not to be a final solution for CO2 reduction in the atmosphere, but provides an achievable solution in the near term while more desirable alternative solutions to power generation can be made economically practical.# ISO certification in India
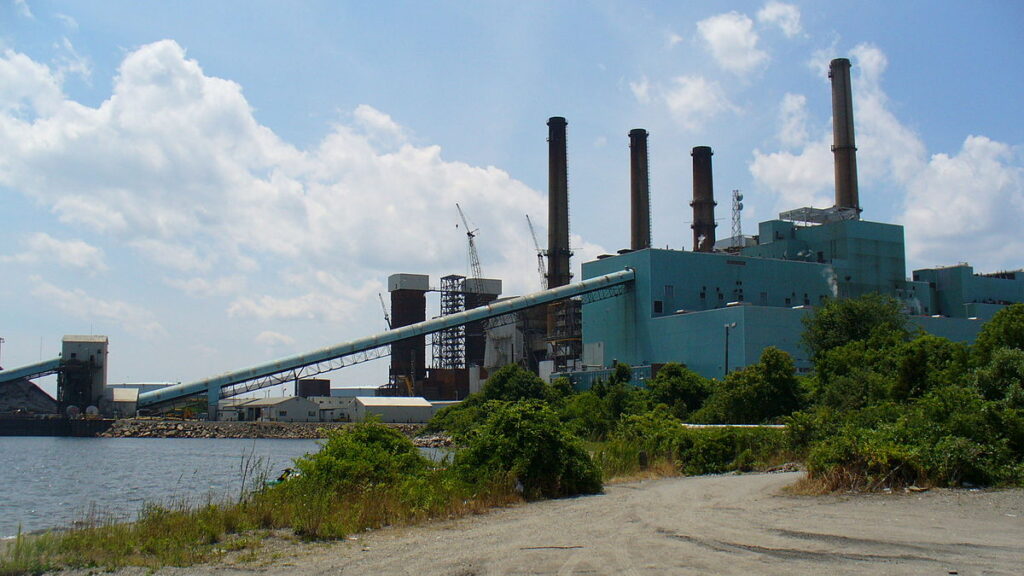
Other examples of oxy-combustion carbon capture are in progress. Callide Power Station has retrofitted a 30-MWth existing PC-fired power plant to operate in oxy-fuel mode; in Ciuden, Spain, Endesa has a newly built 30-MWth oxy-fuel plant using circulating fluidized bed combustion (CFBC) technology. Babcock-ThermoEnergy’s Zero Emission Boiler System (ZEBS) is oxy-combustion-based; this system features near 100% carbon-capture and according to company information virtually no air-emissions. # ISO certification in India
Other carbon capture and storage technologies include those that dewater low-rank coals. Low-rank coals often contain a higher level of moisture content which contains a lower energy content per tonne. This causes a reduced burning efficiency and an increased emissions output. Reduction of moisture from the coal prior to combustion can reduce emissions by up to 50 percent.